Der Kabinenbau war eine spannende Aufgabe, da ich mich mit diversen Themen auseinandersetzen konnte.
So konnte ich mein ‹Know-how› im Arbeiten mit 3D Programmen (Sketchup) vertiefen und stellte fest, dass das Designen der Kabine mir viele Probleme im vorab aufzeigt, bevor wir es umgesetzt hätten. Anderseits kamen mir die einfachsten Lösungen dann, wenn ich direkt vor dem Fahrzeug bzw. Kabine stand und mir die Sache direkt anschauen und anfassen konnte.
Bei der Wahl der Kabinenbauart und der Materialien habe ich einiges über die Vor- und Nachteile von Stahl, Edelstahl, Alu und GFK erfahren. D.h. wie die Materialien sich bei Temperatur verhalten, wie dessen Ausdehnung, Elastizität, Verformbarkeit, Schweiss- , Lackier- und Klebbarkeit und dessen Stressverhalten ist.
Bei der Umsetzung stellte ich bald fest, dass eine gute Schweissnaht nichts mit dem zu tun hat was ich in einem Schweiss-Grundkurs gelernt habe. Ebenfalls musste ich mir eingestehen, dass es in Zürich (Schweiz) und Umgebung sehr schwer ist einen gedeckten und abgeschlossenen Platz zu finden an dem man arbeiten kann.
Nachdem ich diese Tatsache eingesehen hatte, merkte ich, dass auch in kleineren Metallverarbeitungsunternehmen die digitale Transformation stattgefunden hat, diese mit digitalen Daten gleich gut umgehen können wie mit Skizzen und Erklärungen. So kam es, dass ich die Kabine als 3D Modell erstellte und anhand dieser Daten alle Kabinenteile auf einer 3D LaserCutter Maschine herstellen und von Hand zusammenschweissen liess.
Kabinendesign
To the topViel Zeit haben wir in die Recherchen gesteckt um für uns herauszufinden welche Konstruktionsart, Hubdach und Materialien wir beim Kabinenaufbau verwenden wollen.
Hier noch vorab einige Hintergrund-Informationen zur Pinzgauer Wanne.
Kabine
In der Designphase spielten wir diverse Konstruktionsarten wie Koffer-, Platten- und Rahmenkonstruktionen mit verschiedenen Materialien wie Alu, Stahl und Verbundplatten durch und mussten feststellen, dass eine Profil-Stahlrahmenkonstruktion mit Blech für uns die akzeptabelste Lösung sein wird. Bei allen anderen Lösungsvarianten befürchten wir, früher oder später, Spannungsrisse aufgrund der Fahrzeugverwindung zu erhalten. Einen Kofferaufbau wie es der San Pinzgauer hat, wollte ich nicht, da uns dies zu schwer und zu viel Platz weggenommen hätte. Ebenfalls wäre dieser nicht mehr containertauglich gewesen.
Der Grundprofilrahmen besteht aus 4-Kant 1.5 mm dickem, pulverbeschichtetem Stahl in unterschiedlichen Abmessungen. Die Aussenhaut besteht aus 0.8 mm dickem Edelstahlblech.
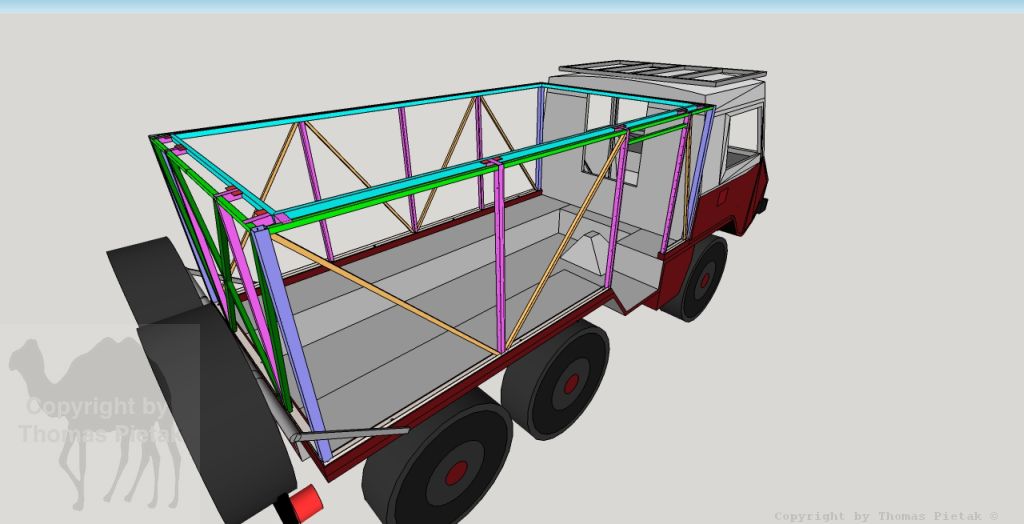
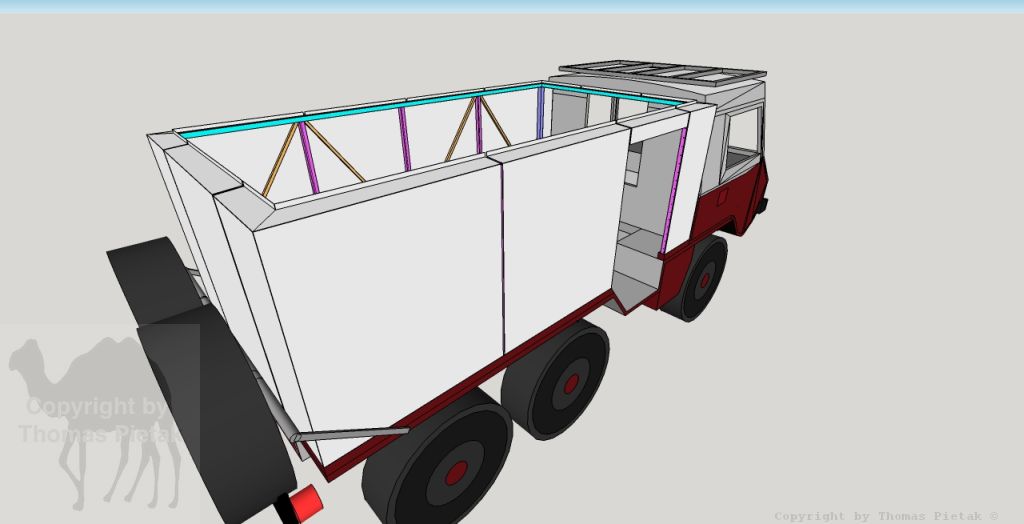
Die Bleche werden auf den Grundrahmen geklebt. D.h. ohne Nieten, Schrauben oder Schweissen. Dieses Vorgehen hat den Vorteil, dass durch den Kleber das Blech zum Grundrahmen eine Fahrzeugverwindung zulässt.
Ich muss gestehen, dass ich eine Konstruktion, wie ich sie mache, bis jetzt nirgends 1:1 gefunden habe. D.h. Kleben der Aussenbleche ohne zusätzliche mechanische Fixierung (z.B. Nieten, Schrauben, Schweissen) auf einen Profilrahmen der keine hintere Tür hat, sich aber dennoch um einige cm verwinden können muss.
Inwieweit sich dies bewähren wird, werden die nächsten Jahre zeigen.
Metrialwahl
Bei der Wahl der Materialien bin ich für den Grundrahmen beim Stahl gelandet und bei Edelstahl für die Aussenbleche.
Stahl ist zwar 3 mal schwerer wie Aluminium, doch eine Konstruktion aus Aluminium hätte mir grössere Abmessungen der Grundrahmenkonstruktion ergeben, welche die Gewichtsersparnisse zum Teil wieder wettgemacht hätte. Ebenfalls stellte ich bei den Kleber Recherchen (technischer Industriekleber) fest, dass Kleben von unbehandeltem Aluminium (–> Oxidation) nicht unproblematisch ist. Edelstahl für den Grundrahmen kam auch nicht in Frage, da die Elastizität (E-Modul) bzw. Verformbarkeit von Edelstahl sehr viel schlechter ist als Stahl (spröder). Für die Aussenhaut ist Edelstahl jedoch eine gute Lösung, da die Bleche keine grösseren Kräfte aufnehmen müssen.
⇒ Grundrahmen: Stahl E235 mit Pulverbeschichtung
⇒ Aussenhaut: Edelstahl Blech 0.8 mm
Hubdach
Für uns war und ist es wichtig, ein möglichst kompaktes Reisefahrzeug zu haben um möglichst überall durchzukommen. Sei dies in Städten, Dörfern oder auf engen Wegen, welche durch Gebüsche oder Bäume eingeengt werden. Ebenfalls soll unser Reisefahrzeug containertauglich sein. Anderseits sind wir zur Erkenntnis gekommen, dass mit dem Alter man gerne etwas mehr Komfort und Stehhöhe haben will. Auch bei schlechtem Wetter bzw. in kälteren Regionen ist es angenehm, wenn man es sich im Fahrzeug gemütlich machen kann. Eine Hubkabine wäre da für uns eine gute Lösung. Bedeutet aber erheblich kompliziertere Konstruktion, schwerer und wartungsintensiver als ein Fixdach.
Nach diversen Skizzen und Diskussionen entscheiden wir uns für ein Parallelhubdach mit festen Seitenklappwänden.

Vorteile:
Wandstärke minimal, Tür auch im geschlossenem Zustand benutzbar, Durchgang nach vorne problemlos möglich, gute Lüftungsmöglichkeiten.
Nachteile:
Aufwändige Hubmechanik, Regen- und Staubdichtheit müssen besondere Beachtung geschenkt werden, Gewicht ca. 100 Kg mehr gegenüber einem Fixdach.





Unser Hubdach besteht aus vier Sandwichplatten-Klappwänden die eine Gesamtdicke von jeweils 33 mm haben. Die Sandwichplatten wurden in einen Eichenrahmen eingelassen, damit die Kanten robust gegen Schläge und Witterung sind.
Ebenfalls nimmt der Eichenrahmen die Stangenscharniere und Nut-Einfräsungen auf.
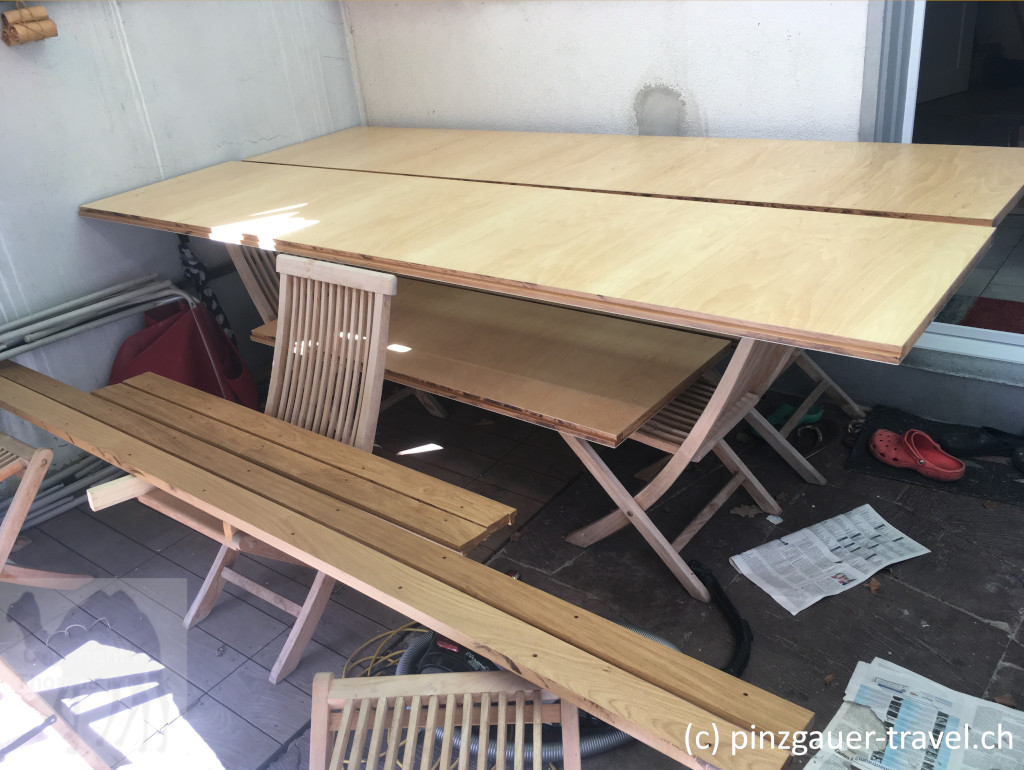
Die Sandwichplatte selber besteht aussen aus 1.5 mm GFK, der Kern aus PUR RG 40 in 27 mm Stärke und innen aus 4 mm Birkensperrholz.
Das Hubdach wird über 4 Hubzylinder um ca 650 mm angehoben, so dass wir innen eine Stehhöhe von ca. 2 Metern haben.
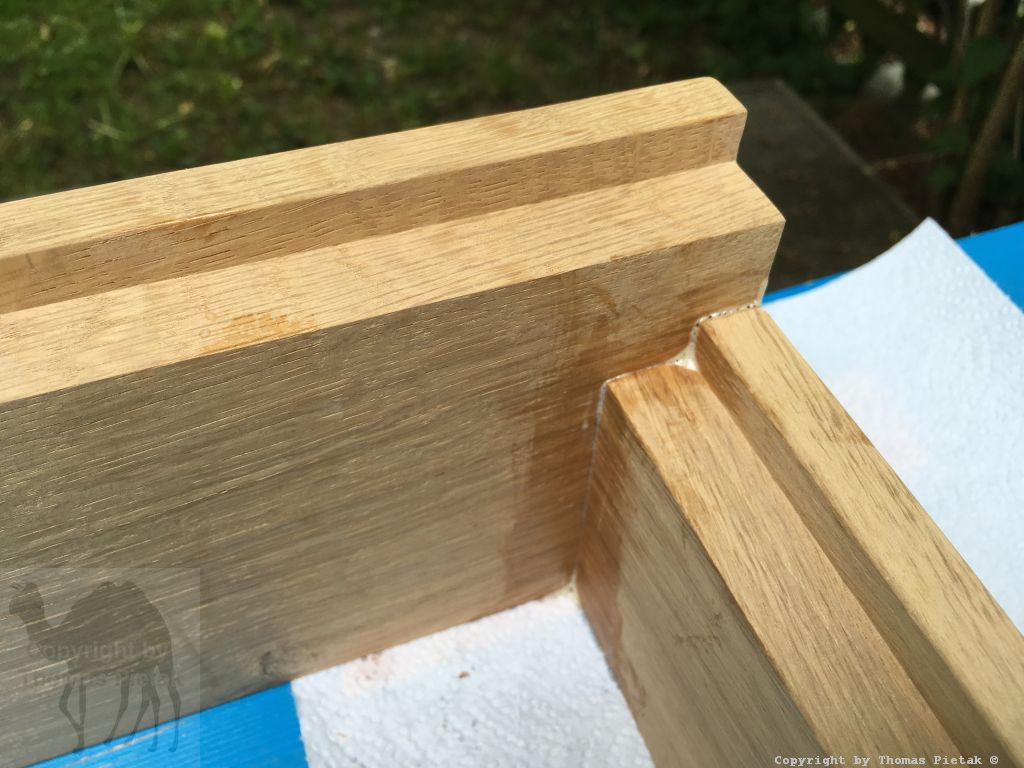
Die Klappwände auf der Stirnseite (vorne, hinten) sind unten an der Kabine an einem Eichenholzrahmen befestigt, welcher die Kabinenöffnung umrahmt. Die Seitenklappwände (links, rechts) sind am oberen Eichenholzrahmen im Hubdach befestigt. Dadurch kann das Hubdach hochgefahren, die Stirnwände hochgeklappt werden und es ergibt sich eine offene Kabine bei welcher die Seitenklappwände nicht im Weg stehen.
Hubdachalternativen
Andere Konstruktionsarten haben wir ebenfalls in Betracht gezogen, doch wieder verworfen, obwohl diese auch ihre Vorzüge haben und eine akzeptable Lösung ergeben hätten.
Hubschachtel
Vorteile:
regendicht, staubdicht, stabile Konstruktion, sicher gegen Diebstahl (Tür, Fenster)
Nachteile:
schwer, doppelte Wandstärke plus Spiel zwischen den Wänden. Tür nur im hochgefahrenen Zustand benutzbar bzw. grosser Aufwand wenn die Tür auch im geschlossenen Zustand benutzt werden kann. Durchgang nach vorne nur mit grossem Aufwand realisierbar.
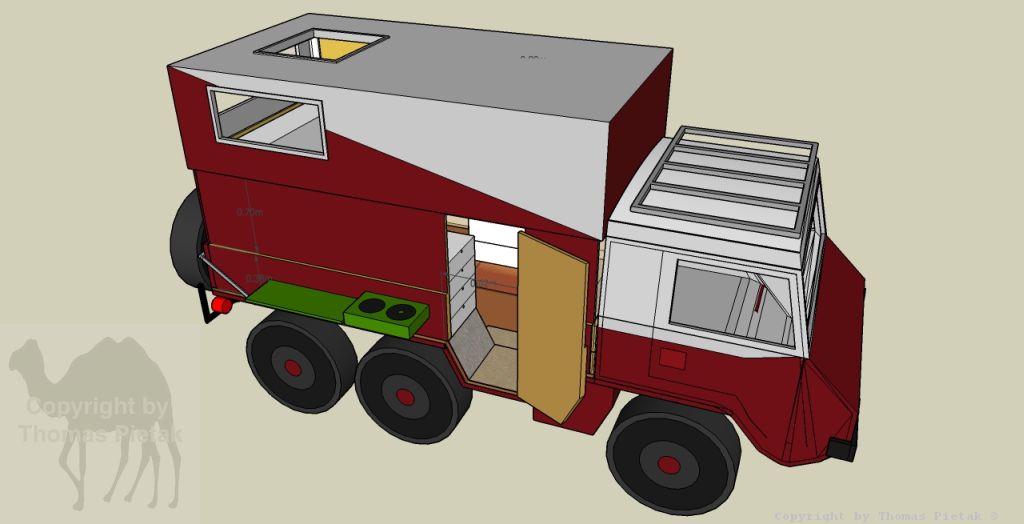
Parallelhubdach mit Stoff
Nach unseren bisherigen Reisen und Erfahrungen sind wir des öfteren sehr froh darüber gewesen, feste Wände zu haben und nicht nur durch einen Stoff mit den diversen Gefahren (Tiere, Menschen) getrennt zu sein.
Aufstelldach
Eine Kante fix mit Scharnier.
Eine sehr stabile Lösung wenn man Stoff für die Seitenwände verwendet. Bei festen Stellwänden wird es allerdings problematisch und man hat ähnliche Probleme wie bei einem Parallelhubdach. Ausserdem hat man nicht über die gesamte Fahrzeuglänge Stehhöhe was wiederum nicht unseren Wünschen entspricht.
Grundrahmen
To the topBeim Grundrahmen habe ich mich nach diversen Recherchen für eine Stahlrahmenkonstruktion mit Blech entschieden.
Hintergrund für meinen Entscheid findest du hier Kabinenaufbau Materialwahl.
Material
- Stahl E235
- 4-Kant Profilrohre
- Ecken 40 x 40 x 1.5 R-Profil (violett)
- Seitenstützen 30 x 30 x 1.5 R-Profil (rosa)
- Anschluss 40 x 40 x 3.0 L-Profil (beige)
- Streben 30 x 30 x 1.5 R-Profil (grün)
- Querstreben 30 x 30 x 1.5 R-Profil (gelb)
- Zuschnitt : Profilrohr Zuschnitt mit LaserCutter
- Korrosionsschutz: Pulverbeschichtung
- Gewicht: ca. 50 Kg
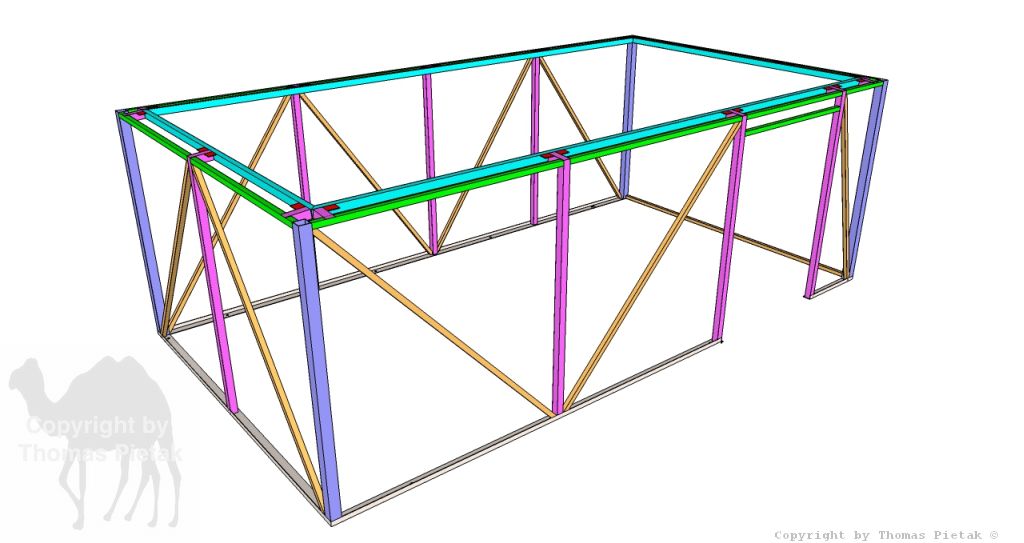
An dieser Stelle will ich noch erwähnen, dass ich lange mit mir gerungen habe, den Rahmen selber zu schweissen. Da ich nur sehr wenig Erfahrung in der Metallverarbeitung, keine eigene Werkstatt und keine Schweissanlage habe, musste ich mir eingestehen, dass es einfacher, preislich billiger und qualitativ ein viel besseres Ergebnis geben wird, wenn ich die Herstellung extern in Auftrag gebe.
Zusätzlich kommt noch dazu, dass der ganze Aufbau millimetergenau ist, was mir später viel Arbeit einsparte.
Die einzelnen Profile sind mit Laschen und Aussparungen versehen, so das die Profile zum Gesamtrahmen zusammengesteckt werden können. D.h die Schweissarbeiten sind innerhalb von kürzester Zeit möglich, was wiederum die Kosten senkt.
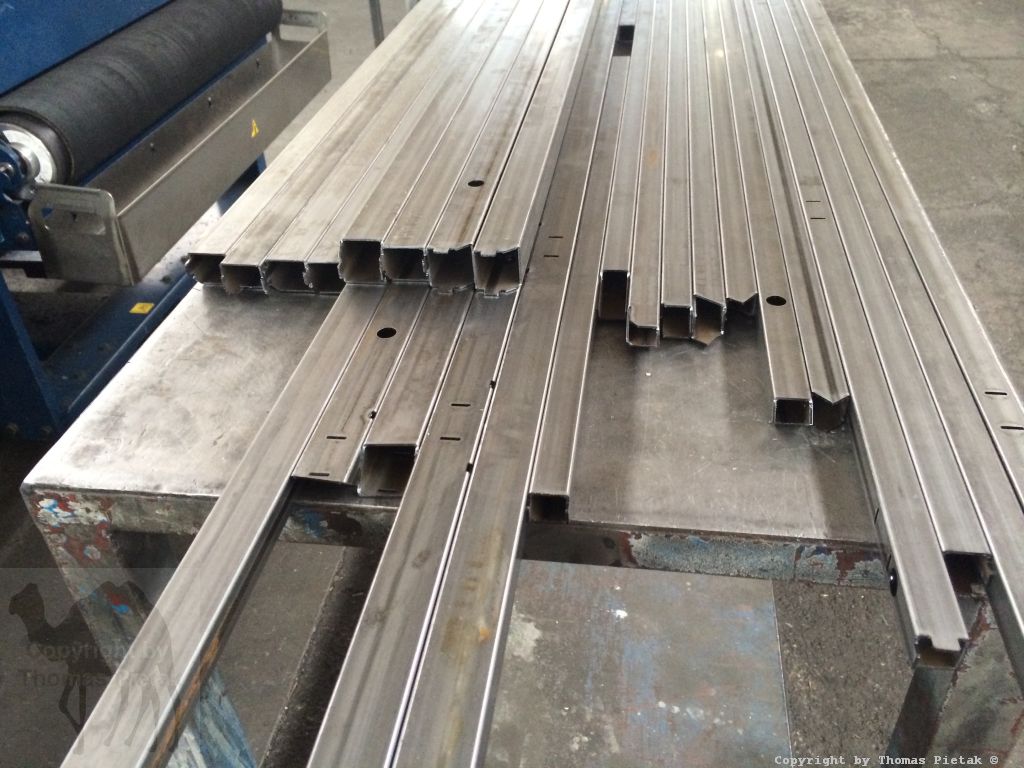
Das Endergebnis kann sich sehen lassen.
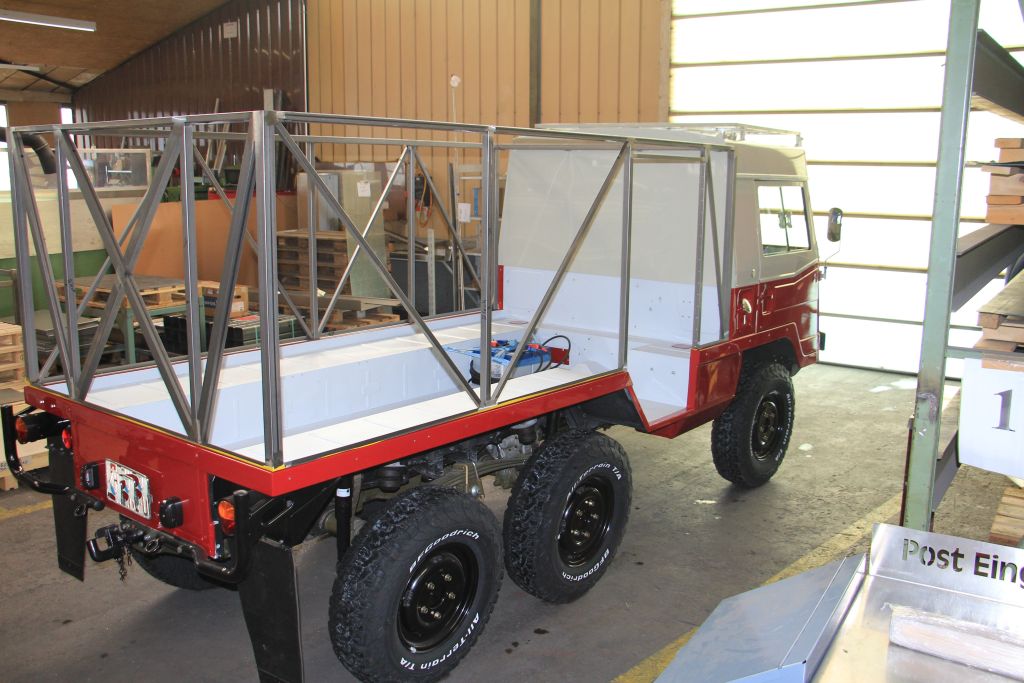
Aussenblech
To the topDa der Grundrahmen bereits als 3D Modell erstellt ist, war es noch eine kleine Sache das Aussenblech entsprechend zu zeichnen. Grössere Fragen gab es bei den einzelnen Blechgrössen und der Befestigungstechnik.
Material
- Rostfreier Stahl V2A (0.8 mm Dicke)
- Zuschnitt mit LaserCutter
- Biegen, Schweissen
- Gewicht: ca. 60 kg (inkl. Kleber)
Bezüglich der einzelnen Blechgrössen habe ich mich aufgrund der Wärmeausdehnung und der Verwindungen dafür entschieden kleinere Bleche zu verwenden und nicht solche die über die gesamte Länge des Fahrzeuges gehen.
Dieser Entscheid war gut, da Bleche von 3 Meter Länge für mich nicht mehr handelbar gewesen wären. Dünnere Bleche wären von der Festigkeit her möglich gewesen, doch ohne Sicken oder andere Versteifungen innerhalb des Bleches schwerer zu verarbeiten bzw. zu schweissen.
Bei der Befestigungstechnik wollte ich keine Nieten bzw. Schrauben im Aussenblech haben. Schweissen war auch keine Option, da sich Edelstahl mit E235 Stahl nicht gut schweissen lässt und ich dadurch den Rostschutz der Pulverbeschichtung beschädigt hätte.
Für die Befestigung der Bleche auf den Grundrahmen habe ich mich nach diversen Fahrzeugbesichtigungen und Telefonaten mit Klebeherstellern entschieden es zu wagen und die Bleche auf den Grundrahmen mit Sikaflex 265 zu kleben!
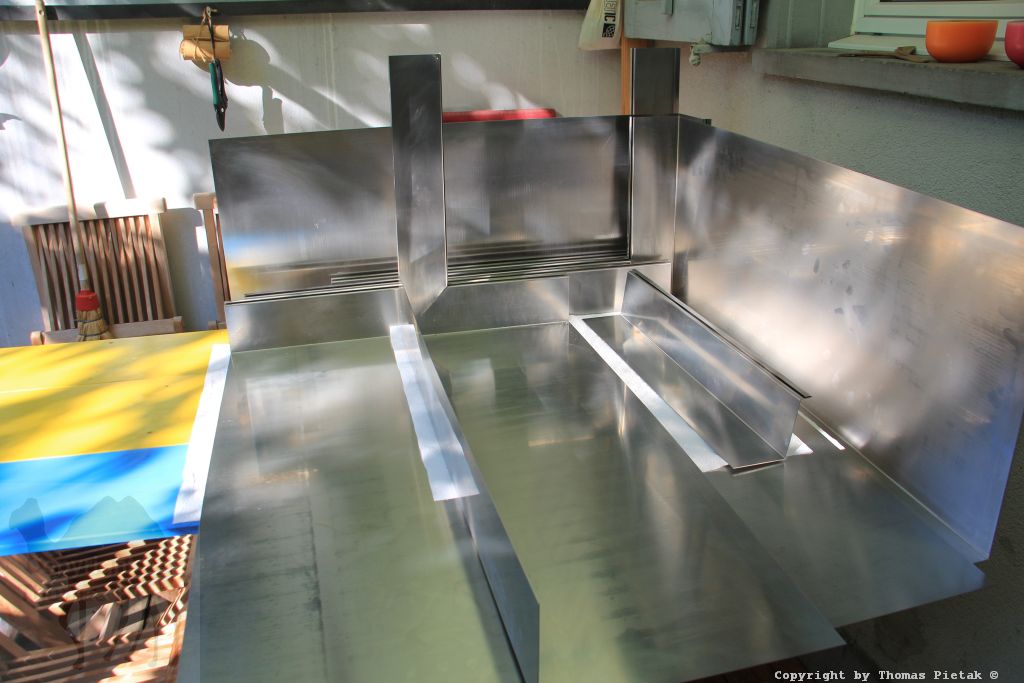
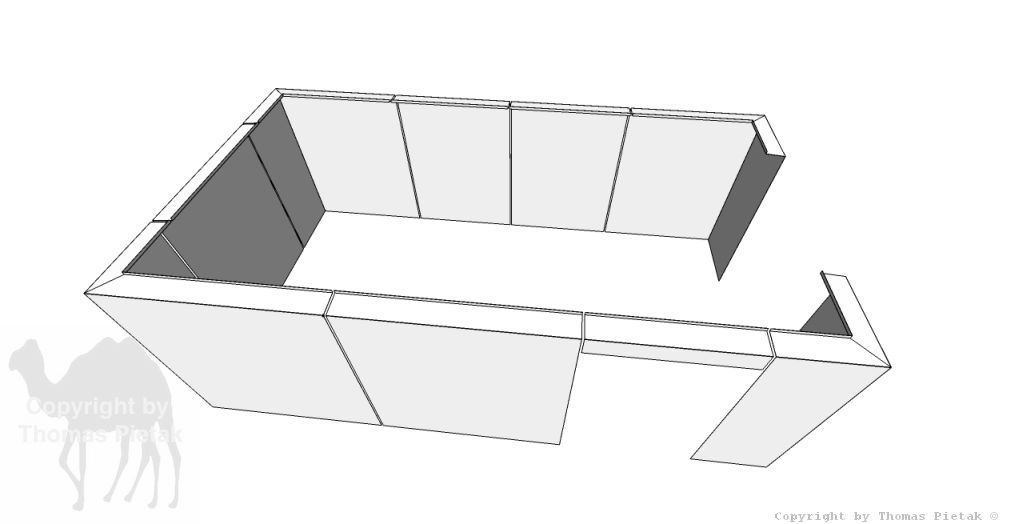
Kleben
To the topKleben des Grundrahmens mit dem Aussenblech
Beim Kleber fiel meine Wahl auf Sikaflex 265. Nicht nur weil dieser alle technischen und mechanischen Anforderungen abdeckt, sondern vor allem wegen der sehr guten Beratung durch Sika (Technischerer Berater). Dieser hat mir die Vor- und Nachteile der einzelnen zu klebenden Materialien aufgezeigt (Stahl, Stahl-Verzinkt, Edelstahl, Pulverbeschichtung, Alu, Alu Eloxiert, 2K-Lackierung, …). Ebenso bei der Wahl des optimalen Klebers, Grundierung, Primer und der Arbeitsschritte die notwendig sind.
Zu klebende Materialien
- Grundrahmen Stahl E235 pulverbeschichtet
- Aussenblech V2A Edelstahl
- 4 mm Dicke und ca 30 mm Breite Klebefuge
Verbrauchsmaterial
- Isopropanol oder Azeton
- Schleiffliess SVF (M3 Scotch grün)
- Sika Aktivator SA100
- Sika Primer 206 GP
- Melaminschaum – Sika PowerClean Air
- Distanzstücke 4 mm (Distanzkreuze aus dem Bodenlegen Bereich)
- Fugenglätter
- Seifenlauge zum Abglätten
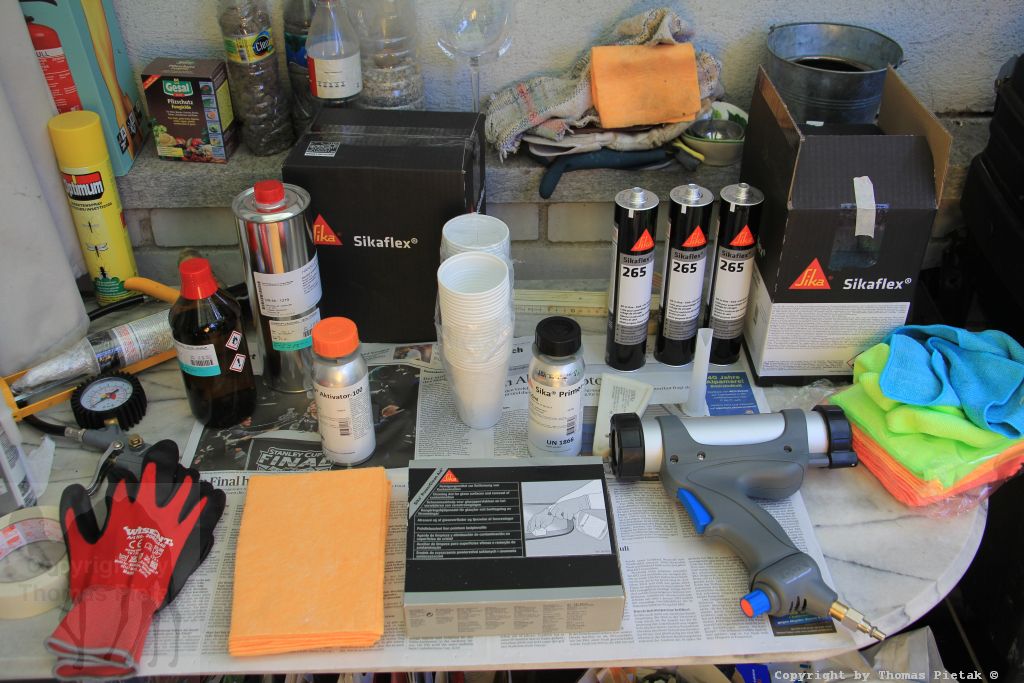
Vorbehandlung
- Pulverbeschichteter Grundrahmen und Edelstahlblech, gleiche Vorbehandlung (Sikaflex Level 3)
- Grundrahmen und Blech mit Isopropanol reinigen
- Anschleifen SVF mit Schleiffliess M3 Scotch
- Nochmals mit Isopropanol gründlich reinigen
- 5 min ablüften
- Nicht zu klebende Flächen mit Abdeckklebeband abkleben (Blechkanten)
- Aktivator SA100 mit staubfreiem Lumpen fein auftragen
- 10 Minuten ablüften
- Primer 206 GP (schwarz) mit Melaminschau in einem Wisch fein auftragen. (Nur einmal über die Fläche fahren, nicht reiben)
- 20 – 30 Minuten (bis max. 2.5 Stunden) ablüften
Kleben
- Sikaflex 265 in Dreieck-Raupen auftragen. Lufteinschlüsse vermeiden
- Distanzkreuze 4 mm im Abstand von ca. 30 cm anbringen. (In den Kleber eindrücken.)
- Blech in den Kleber auf Endmass drücken.
Dies braucht sehr viel Kraft und muss gleichmässig über den gesamten Klebebereich erfolgen. Am besten eine dicke Holzlatte verwenden. 2 bis 3 Personen sollten dabei helfen die entsprechende Druckkraft aufzubringen. - Prüfen ob Endmass überall erreicht und keine Bauchungen an den Klebeflächen entstanden sind.
- Mit Fugenglätte und Seifenlauge überschüssigen Kleber abziehen. (Dies kann eine grosse Sauerei geben, wenn man nicht geübt ist im Auftragen der korrekten Klebermenge)
- Abdeckklebeband entfernen
- Überschüssigen Kleber mit Isopropanol entfernen
Trocknen
- Sikaflex Kleber trocknen aufgrund der Luftfeuchtigkeit und brauchten je nach Tiefe/Breite des Klebers unterschiedlich lang. In meinem Fall war die Klebebreite 30 mm.
- Da an den Kleber von beiden Seiten Luft / Feuchtigkeit hinkommt, ist die effektive Klebebreite 30 mm / 2 = 15 mm.
- 4 mm ersten 24 Stunden
- 1 mm jeder weiteren Tag
- –> ca. 2 Wochen Trocknungszeit
Innenverkleidung
To the topDas muss Kabinenwand Aufbaut Hö?
- Aussenblech 0.8 mm (V2A Edelstahl)
- Isolation 50 mm (flexibler Dämmstoff)
- Innenverkleidung 4 mm (Birkensperrholz)
Die Gesamtwanddicke beträgt ca. 55 mm. Da der Stahl Grundrahmen aus max. 30 mm grossem 4 Kant-Profil besteht, konnte ich diesen gegen innen mit einer 15 mm dicker Isolation abdecken. Dadurch konnte ich ‹harte› tich für. Kältebrücken vermeiden, bei denen das Wärmeleitende Material (z.b. Stahl) von der Aussenwand bis zur Innenwand führt.
Isolation
Bei der Innenwandverkleidung gab es für mich zwei Aufbauvarianten.
Entweder verkleben mit XPS Platten, was eine sandwichartige, steife Struktur (siehe z.b. Gelber Unimog) ergibt oder eine Variante mit flexiblen, geschlossenporiegem Dämmstoff (z.b. X-Trem, Armaflex).
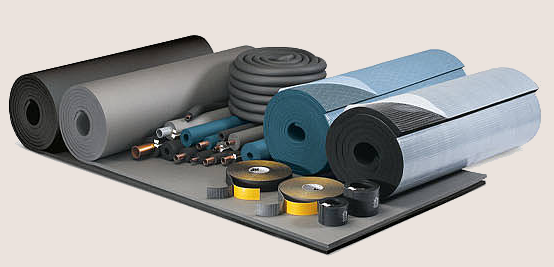
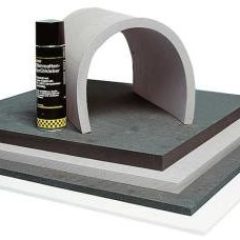
Unsere Wahl fällt auf die flexible Variante.
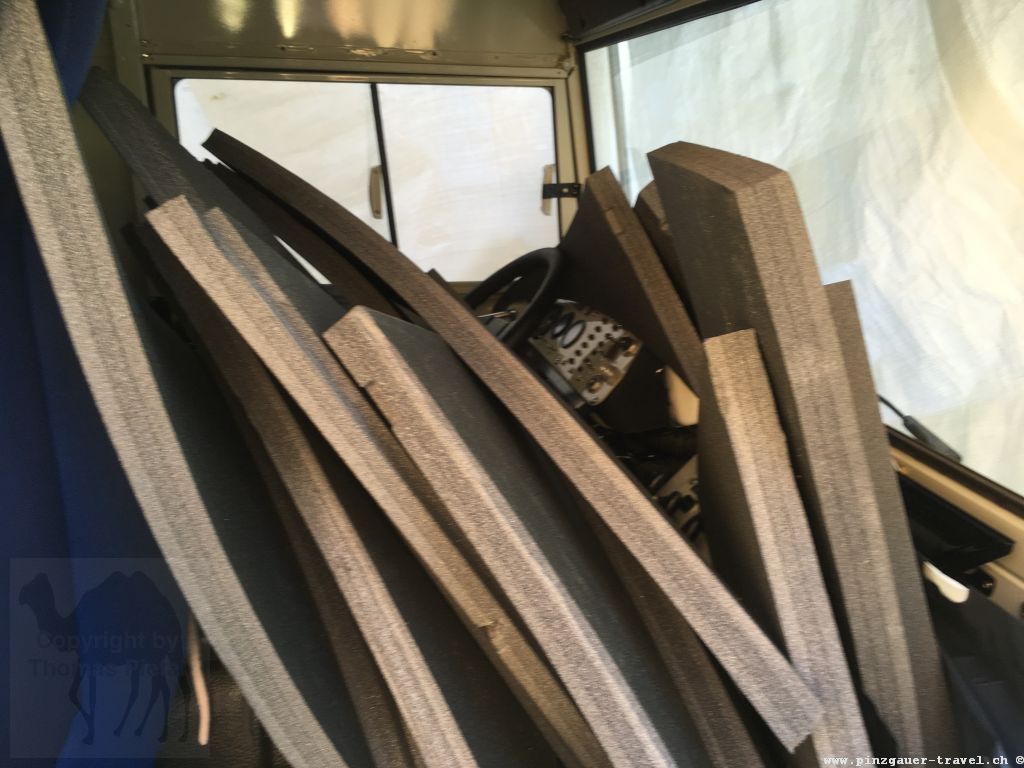
Entscheidend war, dass die Isolation nicht unnötigem Verbindungsstress ausgesetzt ist, keine Quietschgeräusche erzeugt und einfach zu verkleben ist. Ausserdem bin ich weder von aussen noch von innen auf die zusätzliche Stabilität angewiesen die mir eine steife Sandwichplattenkonstruktion ergeben hätte.
Das Aussenblech von 0.8 mm reich vollkommen aus ohne das dieses zusätzlich verstärkt werden muss. Innen wird kein Mobiliar direkt an die Wand geklebt, bzw. verschraubt. Wenn überhaupt etwas direkt an den Seitenwänden befestigt wird, dann erfolgt dies direkt auf dem Grundrahmen auf entsprechenden Befestigungspunkten.
Bei der Isolation habe ich darauf geachtet, dass ich auf den Grundrahmen mindestens eine 15 mm Isolationsschicht auftragen konnte.
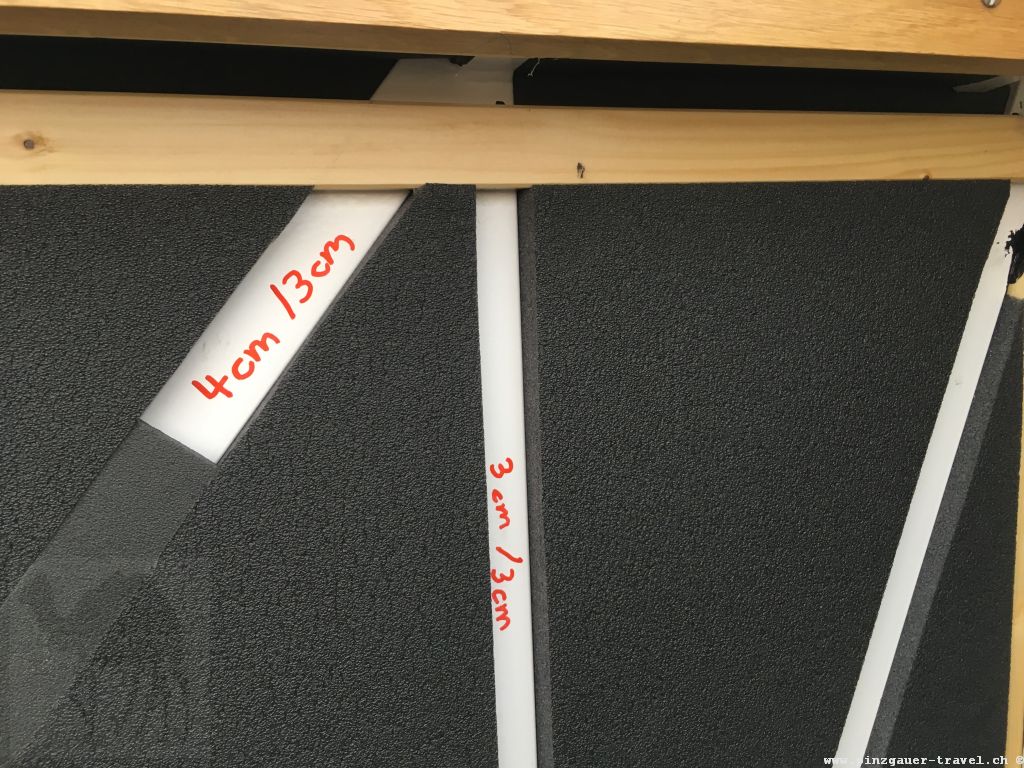
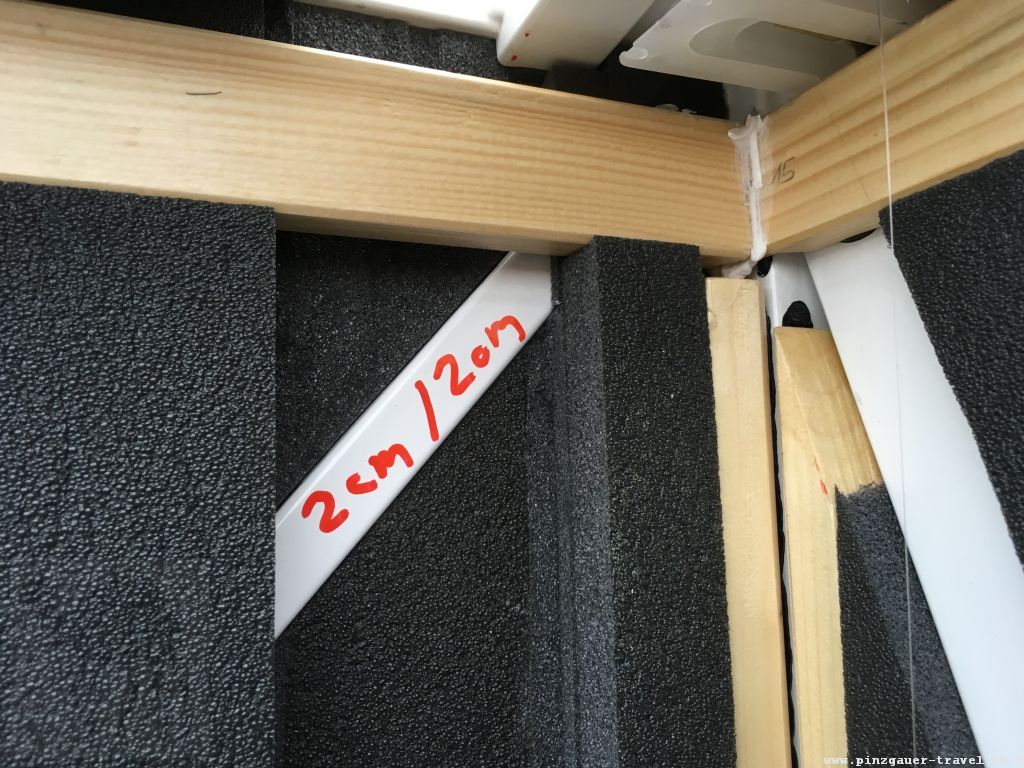
Bei der Montage habe ich X-Trem Platten mit einseitiger Klebefolie verwendet und wo nötig mit Kontaktkleber nachgeholfen. (Plattendicken: 20 mm selbstklebend, 30 mm, 5 mm)
Kontaktkleber: Aus meinen früheren Erfahrungen und Klebetests, kann man sich nicht auf die Temperaturfestigkeit von Kontaktklebern verlassen. So sind auch Hochtemperatur Kontaktkleber die bis zu 110° Grad aushalten sollten nicht gerade das was ich erwarten würde. D.h. bei 80° Grad ist meistens nicht mehr viel von dessen Klebekraft vorhanden und die Teile lösen sich.
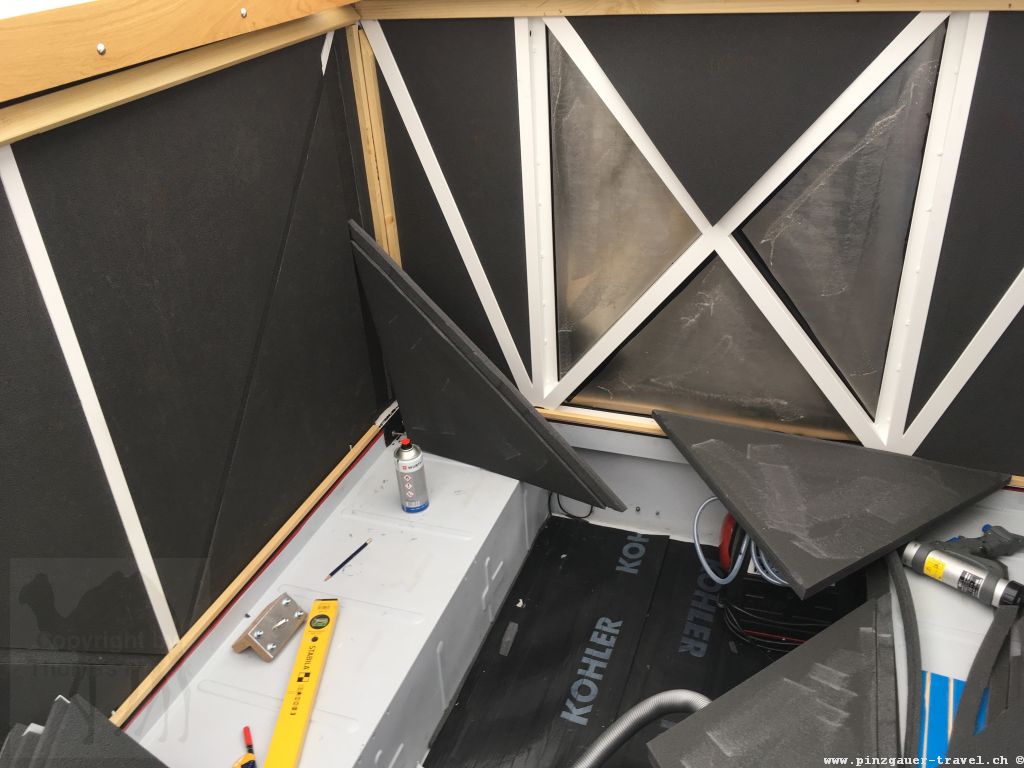
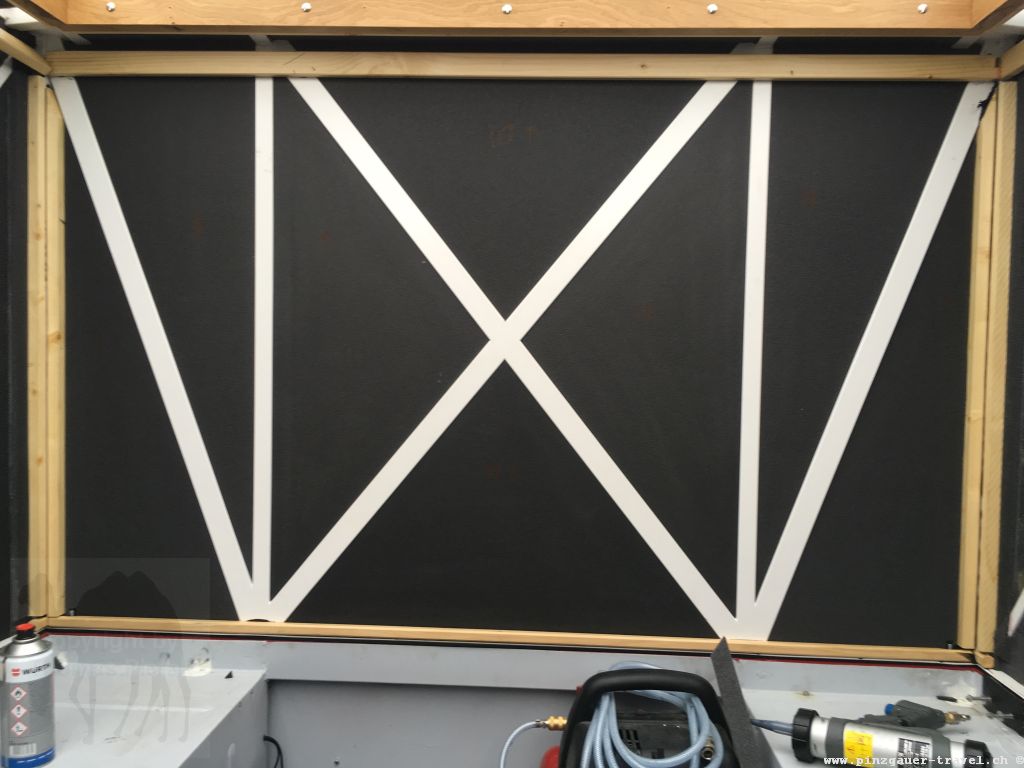
Innenverkleidung
Bei der Innenverkleidung gab es mehrere Aspekte zu beachten. Neben dem Material, welches langlebig und auch nach 10 Jahren noch ansehnlich sein soll, wollten wir eine Wandbeschaffenheit bzw. Farbe die nicht aufdringlich ist, anderseits aber auch nicht langweilig wirkt. Ausserdem muss sie leicht, zahlbar und gut verarbeitbar sein.
Mögliche Materialien:
Vollkern-Kunstharzplatten (z.b. Resopal), GFK, Sperrholz, …
Wir entscheiden uns für wasserfest verleimte Birkensperrholzplatten in 4 mm Dicke.
Um die Birkensperrholzplatten zu befestigen, in meinem Fall habe ich diese mit Sikaflex 265 geklebt, habe ich auf dem Stahl-Grundrahmen an allen Kanten eine Holzleiste aufgeklebt. Auf diese Holzleiste wurde einerseits die Sperrholzplatte geklebt und anderseits konnte ich dadurch kleinere Korrekturen machen damit die Sperrholzplatte bündig auf der Isolation aufliegt.
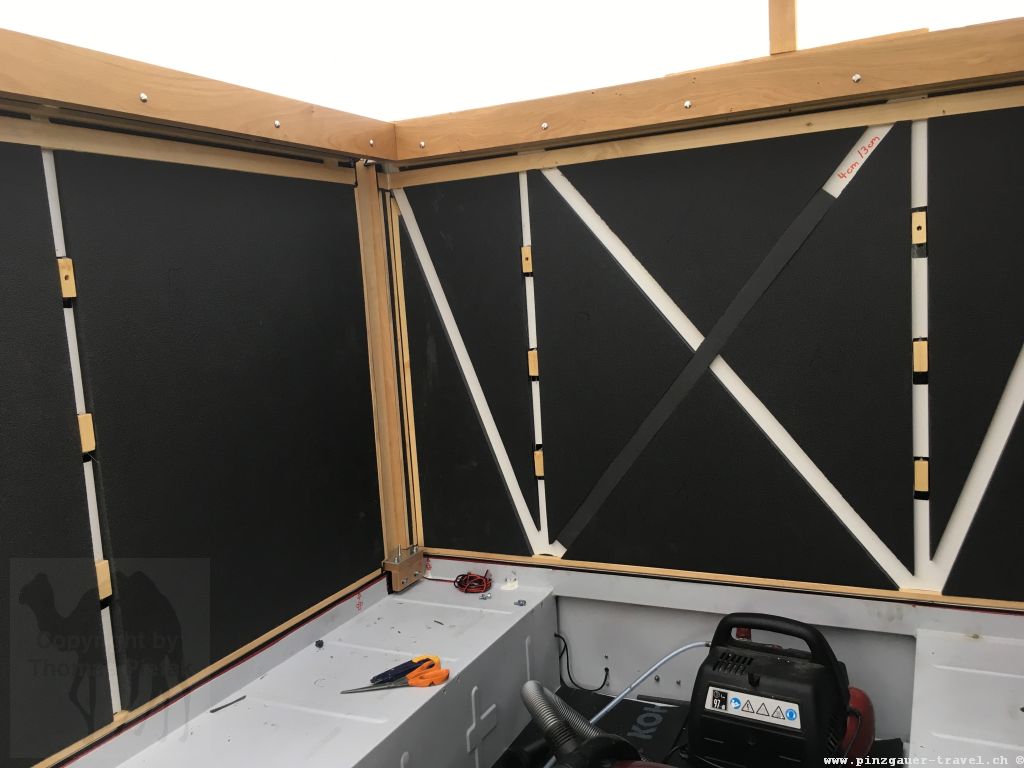
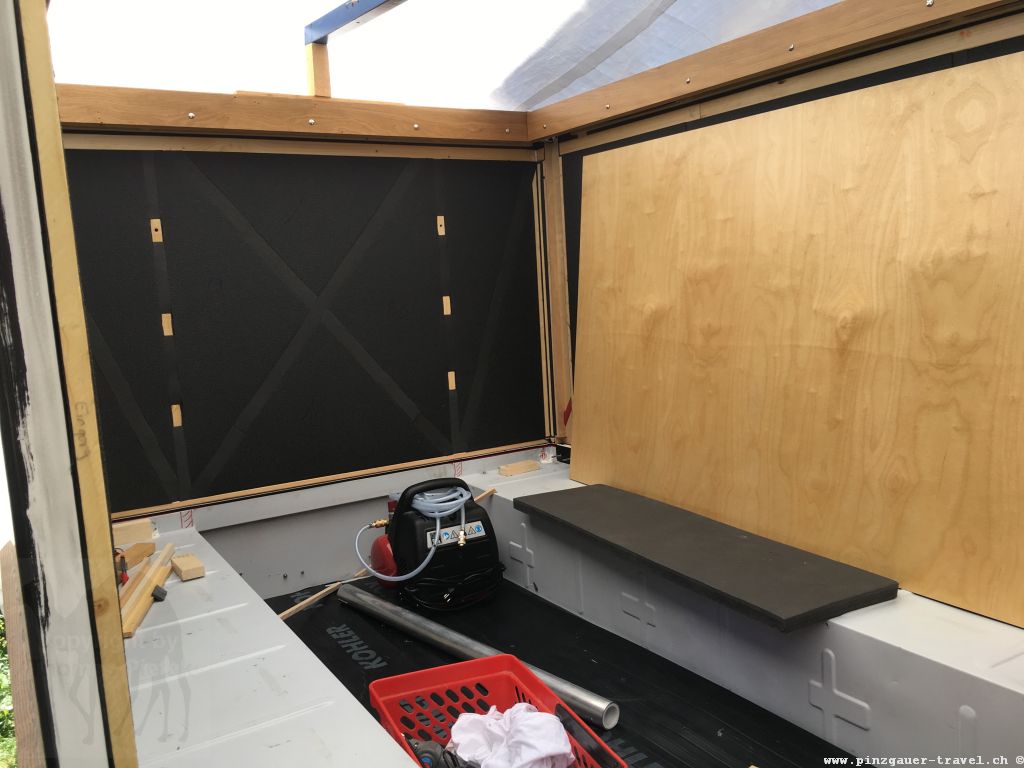
Zusätzliche Befestigungspunkte (Holzklötze) auf dem Grundrahmen mit M6 Nietmuttern sorgen für zusätzlichen Halt für die Sperrholzplatten und ermöglichen
Inneneinrichtung an der Wand zu befestigen ohne das diese die Isolation zusammendrückt.
Lackierung
Die Birkensperrholzplatten habe ich insgesamt 4 mal mit Bootslack lackiert. Inklusive Zwischenschliff.
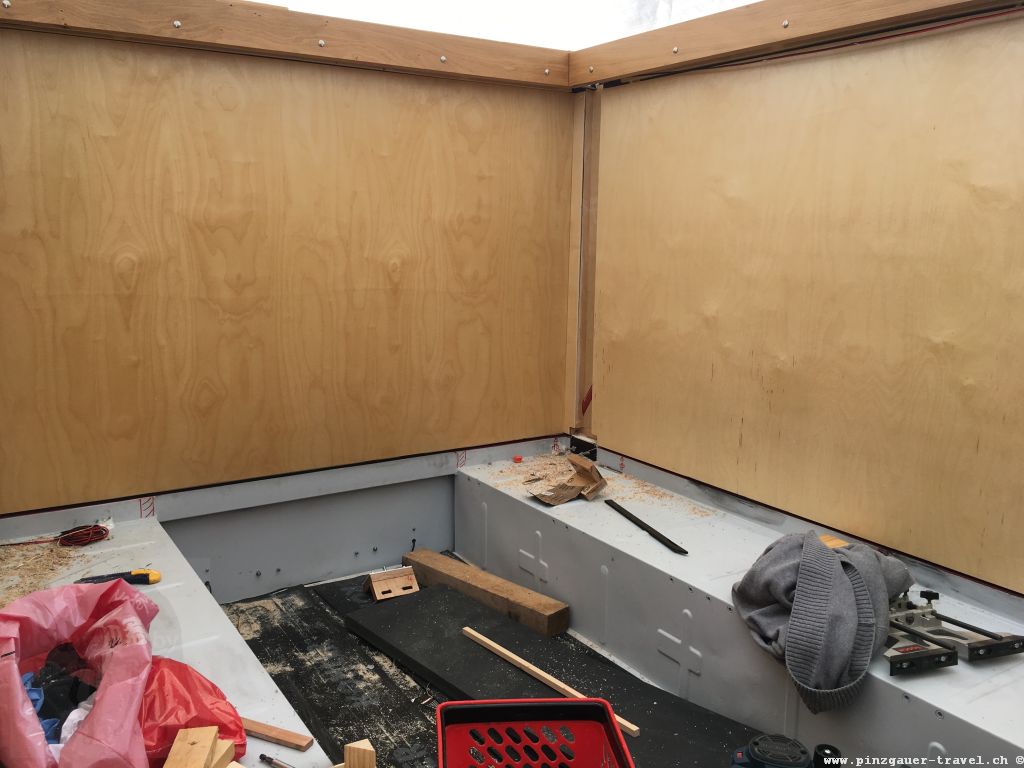
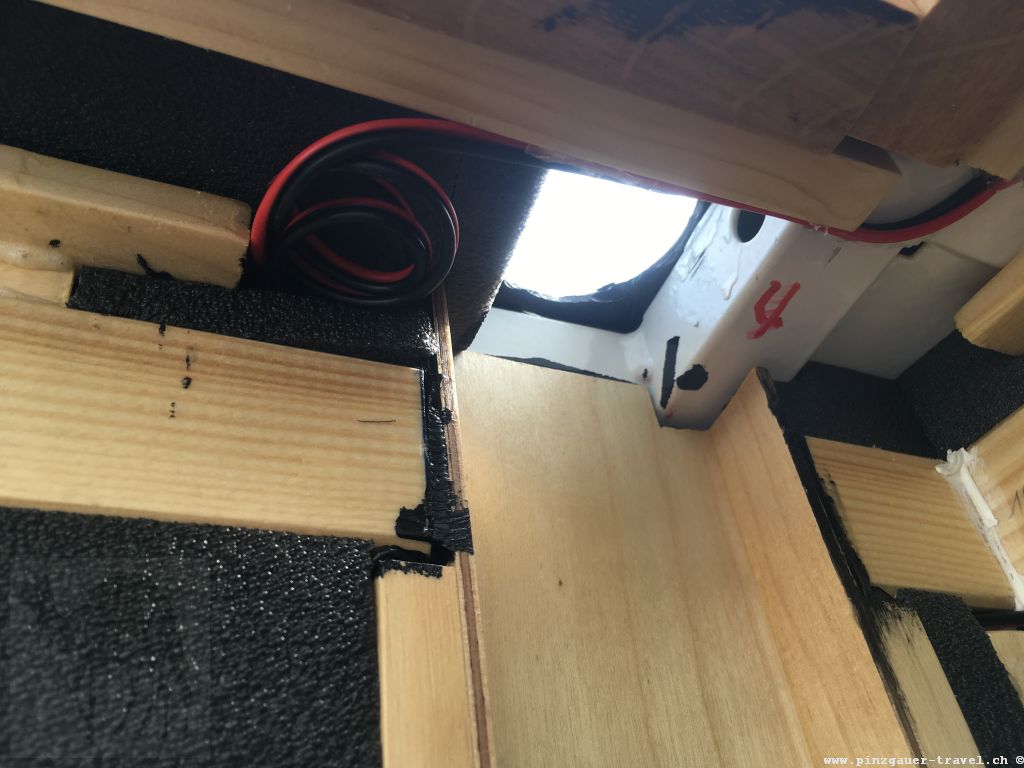
Material
- Lack: International Goldspar Satin (nur für Innenbereich, leider nicht UV beständig)
- Verdünner: International Verdünner Nr 1
- Rollen
Vorgehen
- Erste Lackschicht mit 20% Verdünner Nr 1
- Zwischenschliff Körnung 120 / 180 & Staub entfernen (Staubsauger)
- Zweite / Dritte Lackschicht (jeweils im Abstand von einem Tag)
- Zwischenschliff 180 & Staub entfernen (Staubsauger)
- Vierte Lackschicht (jeweils im Abstand von einem Tag)
Das Ergebnis lässt sich sehen!
Der Lack lässt sich sehr gut verarbeiten und bringt ein hervorragendes Resultat.
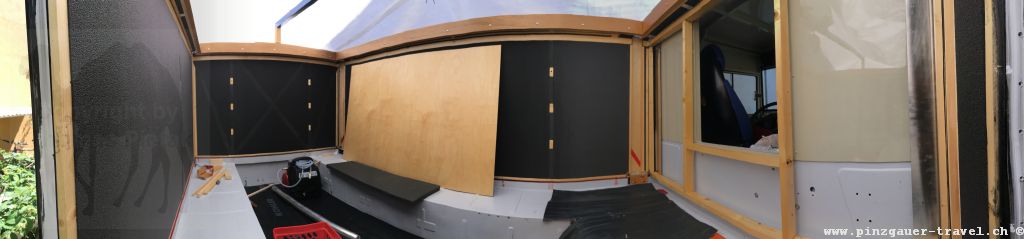
Hubdach
To the topDas Hubdach war eine der grösseren Herausforderungen für mich. Nicht nur der Entscheid ob es ein Hubdach nach dem Hutschachtel-Prinzip oder eines mit Klappseitenwänden werden soll.
Wir haben uns am Ende für die Variante mit den Klappseitenwänden entschieden. …
Das Hubdach besteht aus zwei separaten Hauptteilen, dem Unteren Rahmen- der mit dem Dach des Fahrzeuges verbunden ist – und dem Oberen Rahmen – der die seitenwände und das eigentliche Dach trägt.
Unterer Rahmen:
Der Untere Rahmen besteht aus vier Eichenholzplatten. Diese wurden zuerst mit dem Sikaflex 220 fixiert und dann mit Schrauben an das Fahrzeugdach geschraubt. Diese Platten weisen eine Stufenfräsung auf, welche die Seitenwände bei ausgefahrenem Hubdach fixieren.
Oberer Rahmen:
Der Obere Rahmen besteht wie der Untere aus Eichenholz, diese wurden aber zusammengeschraubt. Er weist auch wie der untere Stufenfräsung für die Seitenwände auf. Zudem wird dieser auch das Eigentliche Dach und die Seitenwände tragen. Für das hinauf und hinunterlassen sind an den Ecken des Rahmens Henkel an denen die Hubzylinder angreifen.
Seitenwände:
Die Seitenwände bestehen aus Sandwichplatten. Welche aus einem Holzrahmen (27mm), einem PUR Schaumkern, an der Innenseite aus 4mm dicken Sperrholzplatten und an der Aussenseite aus einer 1.5mm dicken GFK Platte. Auch bei diesem gibt es die Stufenfräsung, sodass dieses sich in den beiden Rahmen verkeilen kann.
Die Seitenwände wurden an dem Oberen Rahmen mithilfe von einem Edelstahl Klavierscharnier befestigt.
Der Übergang zwischen Seitenwand und Unterem Rahmen wird mit Mossgummi Dichtungen abgedichtet. An den Ecken der Seitenwände wurden Edelstahl blenden montiert, sodass weder Wasser noch Wind eindringen kann.
Um das Hubdach auszufahren, heben 4 Hubzylinder den Oberen Rahme nach oben. Danach werden die 4 Seitenwände Manuel nach aussen geklappt, wegen der Stufenfräsungen muss der Obere Rahmen durch die Zylinder ein bisschen weiter als benötigt nach oben gehebt werden. Sobald die Seitenwänd ausgeklappt sind, können die Hubzylinder wider eingefahren werden und das Dach steht von selbst.
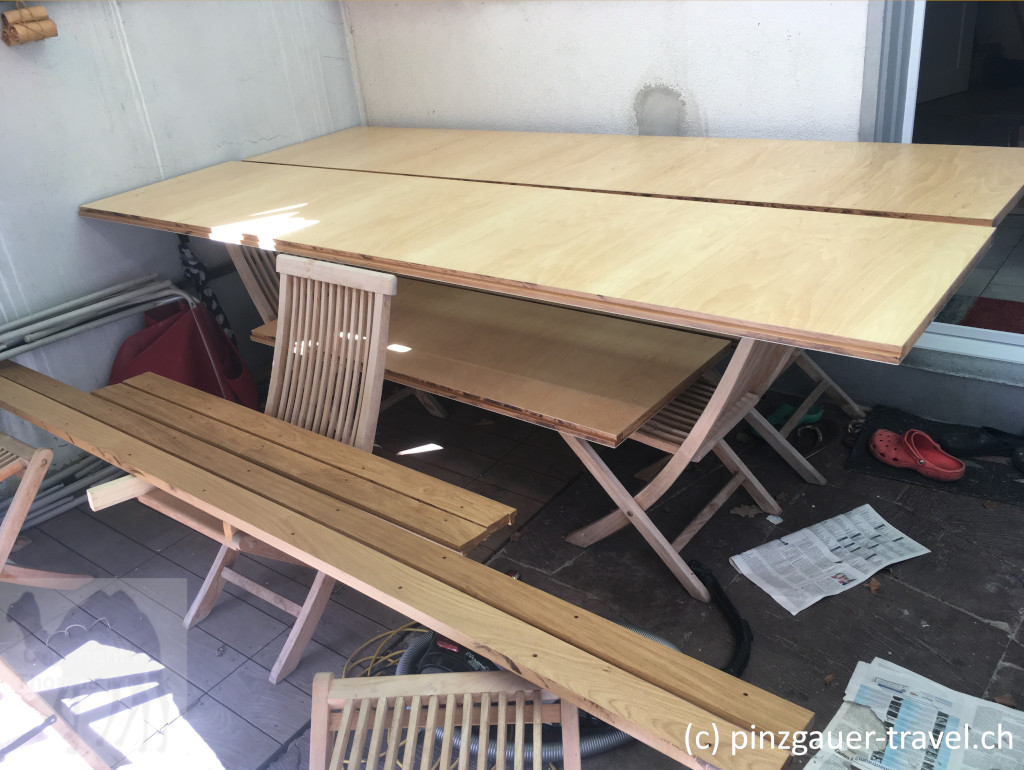
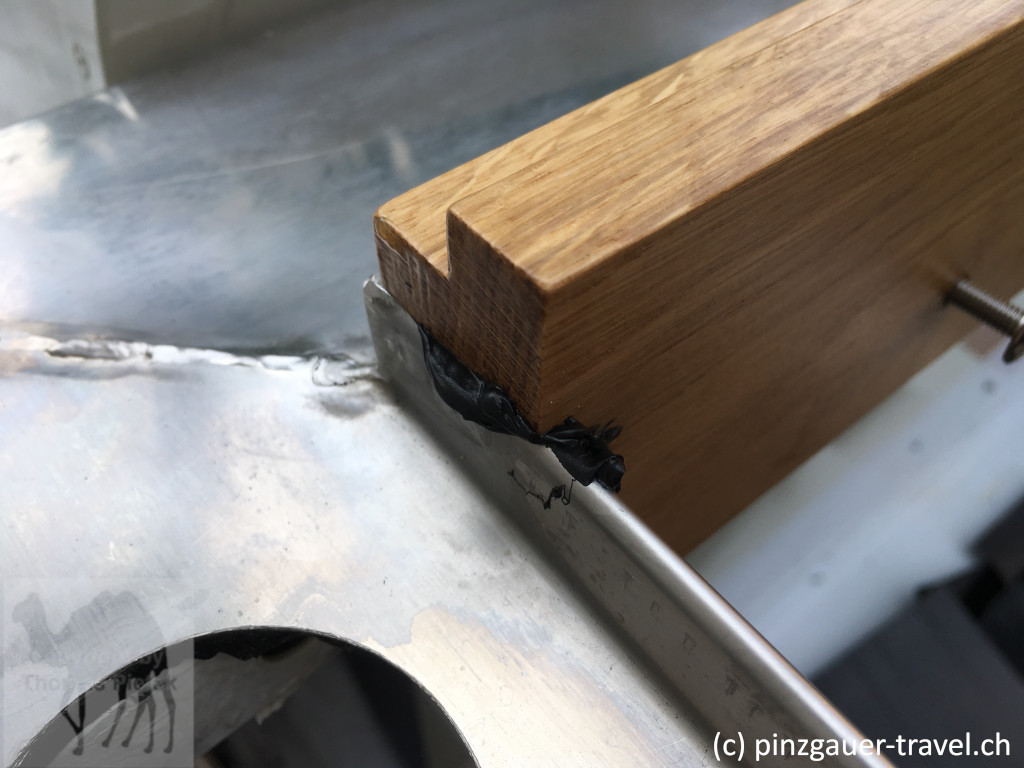
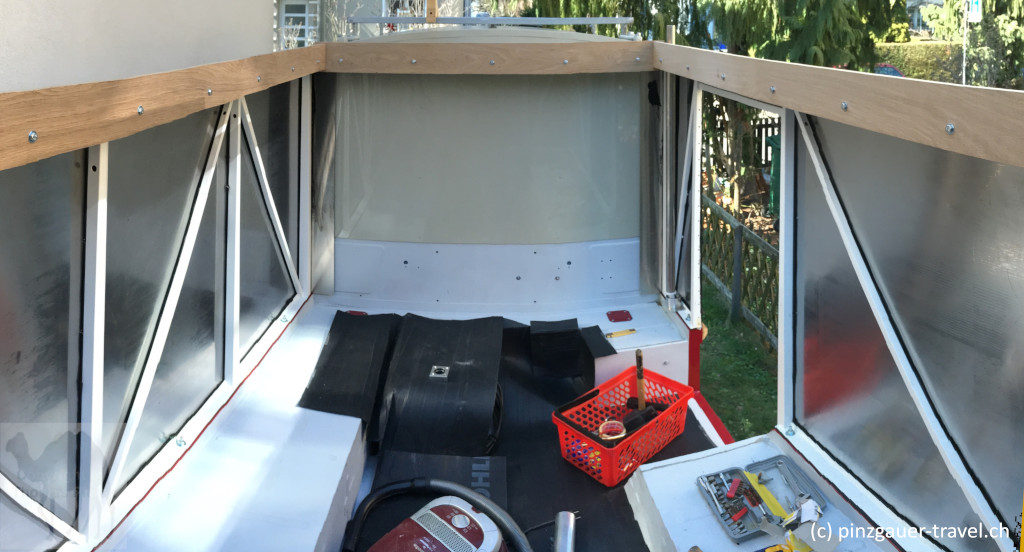
Hubsystem
To the topHubzylinder Lösungen siehe hier
Hubsystem
in Arbeit …